The State of Carbide Compact Formation
Once the carbide compact is formed, it exists in a porous state. During wet grinding, the WC shape undergoes strong impacts, increasing surface energy and reactivity. Longer air exposure leads to greater oxidation, requiring more carbon for reduction. With carbide’s theoretical carbon content at 6.128%, the oxygen-to-carbon ratio is 12/16. For each additional oxygen unit, 3/4 of the carbon is consumed, facilitating η phase formation post-alloy sintering.
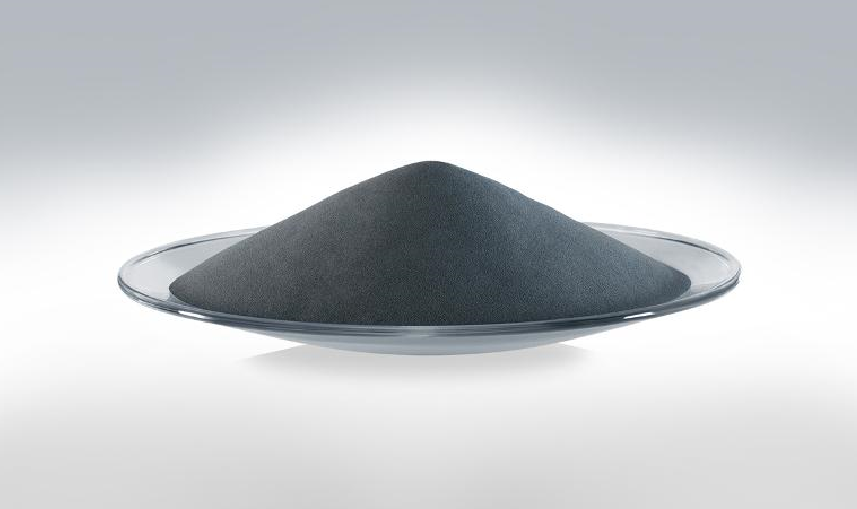
Existence of Oxygen in Carbide Mixtures
Oxygen in carbide mixtures exists as occluded oxygen, cobalt surface oxygen, and oxygen in WO2 or WO3. Total oxygen content is challenging to determine, hindering production. Managing processes effectively is crucial due to ubiquitous oxygen enrichment.
Occluded Oxygen
Found in compact interstices and surfaces, removed by vacuum evacuation before sintering, it doesn’t affect alloy sintering.
Cobalt Surface Oxygen
Forms oxide film due to cobalt’s high susceptibility to oxidation. Reduction during sintering relies on free carbon and combined carbon, impacting carbon-oxygen balance and sintering control.
WO2 or WO3 Oxygen
Some oxides may remain incompletely reduced or oxidized, consuming carbon significantly and complicating sintering carbon content control.
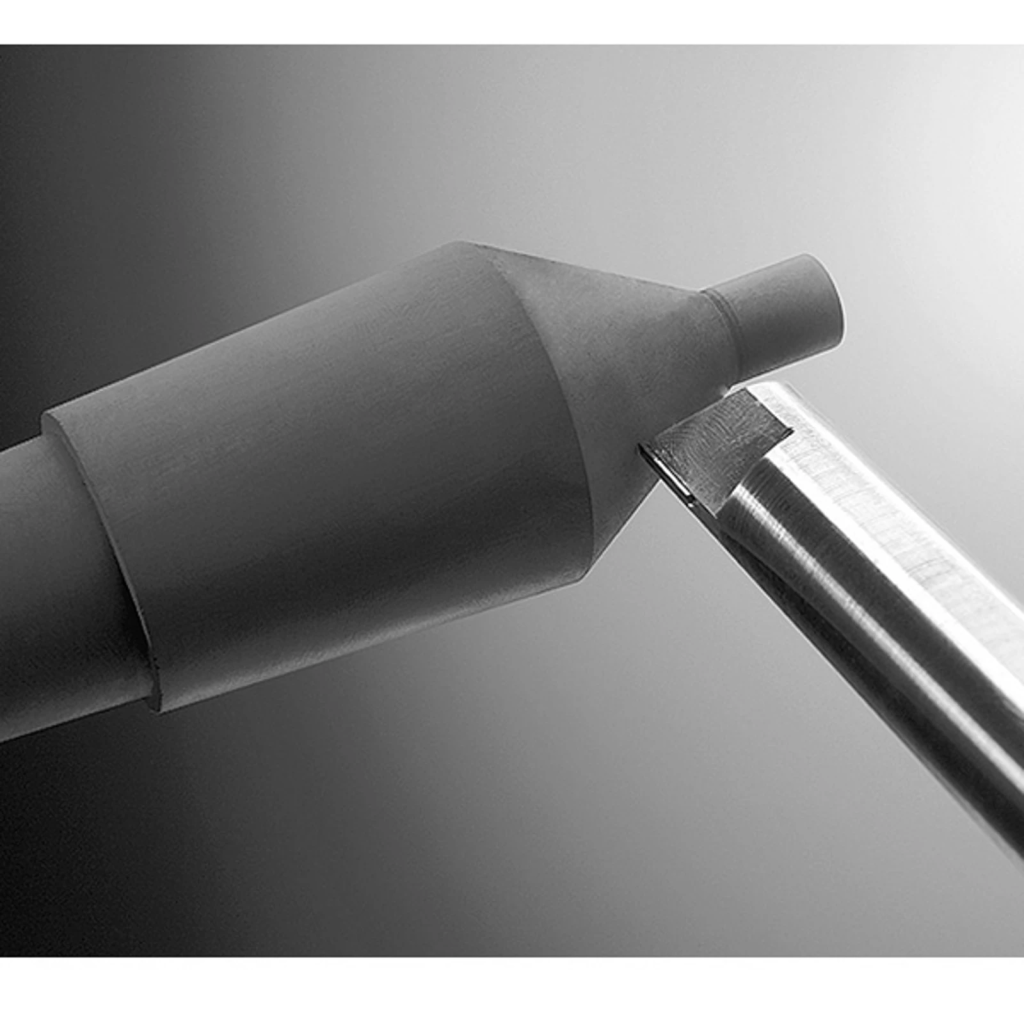
Form of Carbon in Carbide
Carbon exists in WC stoichiometry, carbon increment from binder decomposition, and carbon infiltration from furnace gases. Adjustments are made based on theoretical carbon content and binder decomposition. Carbon infiltration from furnace gases occurs due to graphite product effects, exacerbating at higher temperatures.
Impact of Cobalt on Carbide Properties
Cobalt’s crystal structure affects alloy toughness. ε-Co structure results in lower toughness, while α-Co structure enhances fracture resistance. Cobalt dissolution in WC varies with temperature, affecting slip planes and sintering processes.
Liquid Phase in Carbide
The liquid phase appears theoretically at 1340°C, varying with carbon content. Sintering temperature influences liquid phase amount and grain growth. Inhibitors like VC, TaC, and Cr3C2 can control excessive grain growth.
Conclusion
The pursuit of ternary eutectic structures is crucial in WC-Co carbide sintering, improving durability and toughness. Effective management of WC grain growth and cobalt dissolution without decarburization enhances carbide properties. “High temperature and low carbon” summarize the sintering essence.